Depth of Cut Guidelines
Finishing
- Shoot for around 3%-to-5% of dia. RDOC, no matter how many flutes are on the tool.
- Quick Troubleshooting
- Are you experiencing poor surface finish?
- Check your RDOC, it may be too light of a cut (see #1 above)
- Lower your IPM, Increase your RPM
- Check your tool runout (at end/ corner of tool — with tool mounted in the holder, in the machine) shoot for .0005 TIR max.
- Are you experiencing poor surface finish?
- Tool Life Issues
- Spring passes allow for tool rubbing (lowers tool life) and material work hardening — avoid (or at least minimize of) if possible.
Ramping Angles
- NXG-2: 5-10°
- NXG-3: 5-10°
- NXG-4: 1-10°
- NXG-5: 1-8°
- NXG-6: 1-5°
- NXG-7: 1-3° (caution here)
Note: Lower angles will experience chip thinning and thus allow for higher feed adjustments.
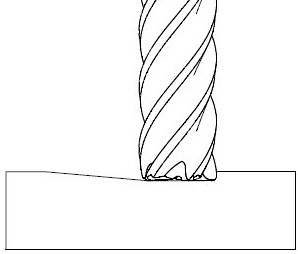
Radial (RDOC) & Axial (ADOC) Depth of Cut
Traditional
RDOC | ADOC | |
NXG-2 | 5% to 50%xD | up to 1.00xD |
NXG-3 | 5% to 50%xD | up to 1.00xD |
NXG-4 | 5% to 50%xD | up to 1.00xD |
NXG-5 | 5% to 40%xD | up to 1.50xD |
NXG-6 | 5% to 30%xD | up to 1.75xD |
NXG-7 | 5% to 10%xD | up to 2.00xD |
D = Tool Cut Diameter
HEM
RDOC | ADOC | |
NXG-2 | NR | NR |
NXG-3 | 8% to 40%xD | up to 3.00xD |
NXG-4 | NR | NR |
NXG-5 | 8% to 30%xD | up to 3.50xD |
NXG-6 | 8% to 20%xD | up to 3.75xD |
NXG-7 | 7% to 10%xD | up to 4.00XD |
D = Tool Cut Diameter
Slot Depth Ranges
NXG-2: up to 2.00xD
NXG-3: up to 2.00xD
NXG-4: up to 1.50xD
NXG-5: up to 0.50xD
NXG-6: up to 0.25xD
NXG-7: Not Recommended
Tips for slotting:
- Follow the chart abo ve.
- Use chip-breaker tools t o
manage chip evacuation. - Ensure good coolant flush,
in direction of the tool’s chip
throw. - Are you less then these
listed ranges? If so, then
there could be room for feed
increase adjustments.