Top Challenges & Strategies to Milling Nickel-based Alloys?
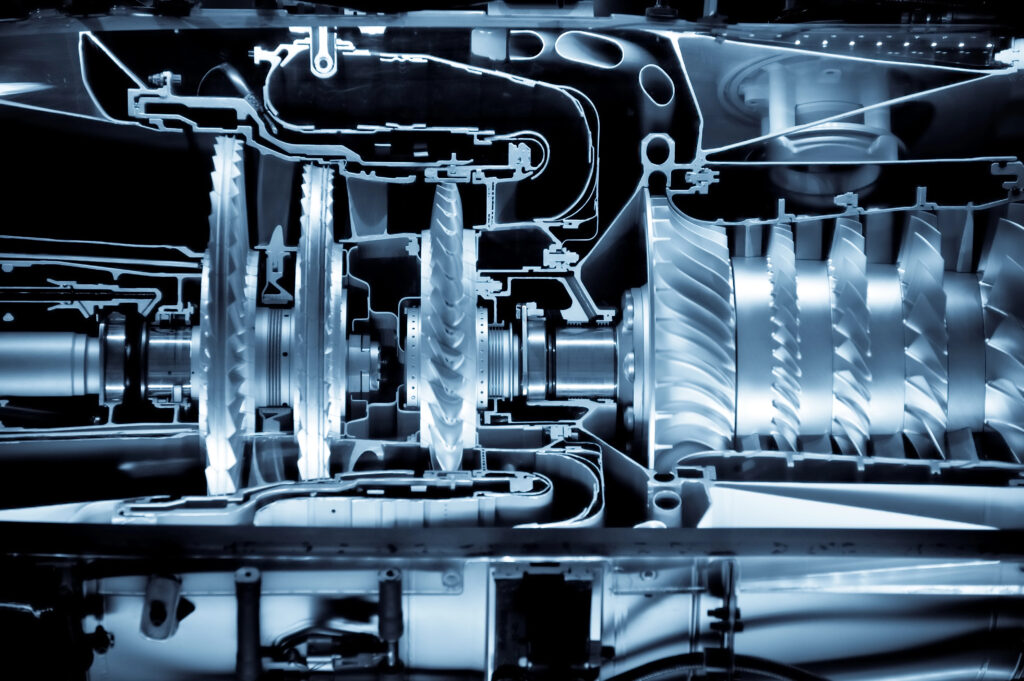
Milling nickel-based alloys, such as Inconel, Monel, and Hastelloy, poses significant challenges due to their unique properties. These materials are prized for their strength, corrosion resistance, and ability to maintain properties at high temperatures, but these same attributes make them difficult to machine.
Key Challenges in Milling Nickel-Based Alloys
1. High Strength at Elevated Temperatures – Nickel-based alloys retain their strength even at high temperatures, resulting in high cutting forces during milling. This increases tool wear and can cause machine deflection or chatter.
2. Work Hardening – These alloys harden rapidly at the cutting zone when subjected to the heat and mechanical stresses of machining. This leads to increased resistance to subsequent cuts, accelerating tool wear and reducing machining efficiency.
3. Poor Thermal Conductivity – Nickel-based alloys have low thermal conductivity (~11-16 W/mK), which means heat generated during machining stays concentrated near the cutting edge, rather than dissipating into the workpiece or chips. This exacerbates tool wear and can cause thermal damage to the workpiece.
4. Abrasiveness – The presence of hard alloying elements, such as chromium, molybdenum, and cobalt, makes these alloys highly abrasive. This accelerates tool wear, especially in uncoated or inadequately coated tools.
5. Chip Formation and Control – Chips from nickel-based alloys tend to form irregular shapes, making them harder to evacuate. Poor chip control can lead to recutting, tool damage, and surface imperfections.
6. Chatter and Vibration – The toughness and ductility of nickel alloys can lead to instability during cutting, especially in less rigid setups. This manifests as chatter, leading to poor surface finish and potential tool damage.
7. Low Cutting Speeds -To prevent excessive heat buildup and tool wear, nickel-based alloys must be machined at lower cutting speeds compared to steels or aluminum. This reduces productivity and increases machining time.
Strategies for Milling Nickel-Based Alloys
- Tool Selection
- Use high-performance tools with coatings like TiAlN, AlTiN, or diamond-like coatings to withstand heat and abrasion.
- Prefer carbide tools or ceramic inserts for enhanced durability and performance.
- Optimized Cutting Parameters
- Use low cutting speeds (10-50 m/min depending on the alloy) with higher feed rates and moderate depth of cut.
- Avoid interruptions during cuts to reduce the risk of work hardening.
- Coolant
- Apply high-pressure coolant directly at the cutting edge to manage heat and improve chip evacuation.
- Rigidity
- Ensure a rigid machine setup and fixturing to minimize vibrations and chatter.
- Toolpath Strategies
- Employ high-efficiency milling (HEM) or trochoidal milling techniques to reduce tool engagement and manage heat buildup effectively.
- Use climb milling whenever possible for smoother cuts and better chip control.
- Tool Inspection and Maintenance
- Monitor tool wear closely and replace tools promptly to avoid catastrophic failure.
- Use largest tool possible to maximize MRR
Milling nickel-based alloys requires balancing productivity with tool life and workpiece quality. Advanced machining techniques and precise process control are essential for success.